Изготовление саба.
Часть 2
Склеивание
Клеил точно так же, блоками. Не
внимая гвозди, отсоединял слои друг от друга, наносил эпоксидную смолу,
прогревал феном и втыкал гвоздики на прежние места. Затем блок еще
немного грел феном и ставил затвердевать под груз. Смолу наносил с
запасом, поэтому излишки обильно выдавливались и приходилось их
зашлифовывать.
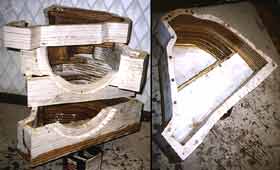
|
Склеенные и "зашурупленные" блоки, для наглядности
поставленные друг на друга вразнобой. Справа нижний блок с
прикрепленным "корытцем", отчетливо видны шляпки саморезов,
выполняющих роль арматуры. |
После склеивания слоев в блоки решил все-таки усилить
конструкцию, а именно армировать ее. Ведь такая фундаментальная на
первый взгляд масса дерева держится фактически на том слое клея, который
скрепляет слои фанеры. А стоит ли ему доверять? Решил не рисковать -
предварительно засверлив отверстия в стенках, ввинтил по 10-12 саморезов
в каждый блок, дополнительно смазав их эпоксидной смолой. Эти саморезы
"прошивают" каждый блок насквозь, исключая тем самым возможные
расслоения фанеры.
Оклеивать стенки ящика стеклотканью не стал
ни в коем случае - не для того я столько времени пилил фанеру, чтобы
потом еще ковыряться со стеклотканью. Однако появилось подозрение, что
фанера может пропускать воздух между слоями и герметизировать стенки
все-таки надо. Поэтому перед соединением блоков между собой их
внутреннюю поверхность я хорошенько прогрел феном, намазал эпоксидкой
так, чтобы она впиталась в поры дерева, а затем продолжать греть ее до
"вставания". Мелкие выбоины и дефекты фанеры замазал замазкой из
ЭДП и опилок. Когда смола затвердела, блоки
склеил между собой, скрепив их, как и раньше, длинными (135 мм)
саморезами в старые отверстия. Не стал приклеивать только верхнюю крышку
ящика.
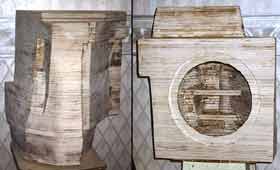
|
Склеенный и грубо зашлифованный ящик, вид сзади и
спереди. Плоскость на лицевой панели уже выведена, вырез под
динамик тоже отфрезерован. |
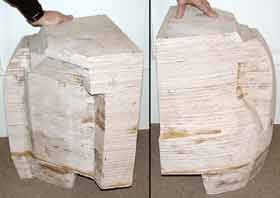
|
То же самое, только вид сбоку :-) Форма, конечно,
достаточно причудливая, но уж так получилось.
|
Когда конструкция высохла, я срезал застывшую смолу и еще
немного обработал поверхности шлифкругом. Теперь самое время заняться
лицевой панелью.
Место под установку динамика
Я
отлично понимал, что создаю себе дополнительные трудности, выбирая схему
передней панели с "утопленным" динамиком. В подиумах эта проблема
решалась просто - склеивались вместе два фанерных кольца, здесь же
углубление нужно было как-то вырезать в
древесине...
Предварительное углубление уже образовалось при
выпиливании слоев, осталось лишь его довести до ума. Для этого я
использовал фрезу и
электродрель. С помощью регулятора глубины сверления (есть такая
дополнительная возможность в дрели) я выставил глубину фрезерования и
постарался выровнять кромки по окружности, остальное снял шлифкругом.
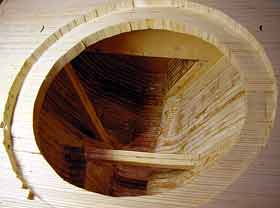
|
Место под динамик после фрезерования. Видно, что
получить ровные кромки по всей окружности не
получилось. |
Однако ручная дрель - не фрезерный станок, поэтому для
окончательной отделки требовалось выровнять и кромку, и посадочное место
под головку. Можно было бы прибегнуть к шпаклевке, но я применил
кардинальный способ. Для этого вырезал из обрезков фанеры кольцо такого
диаметра, чтобы оно свободно помещалось в углублении. Затем оклеил его
бумажным скотчем и смазал литолом. Далее развел эпоксидку с опилками,
нанес ее на лицевую поверхность и аккуратно установил кольцо. После
затвердевания кольцо вытащил, излишки смолы сошлифовал. Эпоксидная
замазка заполнила все неровности и выбоины, в итоге получились
достаточно ровные и поверхность, и кромки.
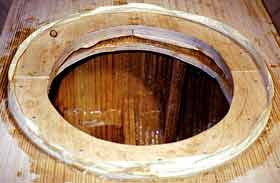
|
Технологическое кольцо в момент затвердевания. Оно
имеет два слоя фанеры в толщину. При установке я не придавливал
его грузом, чтобы плоскость под динамик получилась как можно более
ровная. |
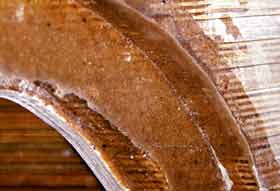
|
Вот какая поверхность получилась после вынимания
кольца. Лицевая кромка еще не обработана, внутреннее кольцо под
динамик не обрезано по диаметру. Образовавшиеся раковины
пришлось зашпаклевать. |
Дополнительно с обратной стороны лицевой панели подклеил
еще один слой фанеры под динамик, а то после фрезерования толщина
посадочного места немного уменьшилась и я решил его
усилить.
Окончательная отделка
Поверхность ящика в
целом получалась достаточно ровной, поэтому особых шпаклевочных работ не
требовала. Однако перед косметическим выравниванием я пропитал внешнюю
поверхность эпоксидной смолой, но уже не так густо, как
внутреннюю.
После шпаклевки и легкого зашкуривания снаружи ящик
выкрасил серой грунтовкой. Внутри же распылил целый баллон серого
антигравия. Когда все высохло, измерил объем ящика водой, получилось
11,5 трехлитровых банок, то есть чуть более 34 литров. Даже удивительно,
как это совпало с расчетами!

|
Грунтовка снаружи, антигравий внутри, поверхности
готовы по окончательную окраску. Светлый ящик в багажнике
кажется таким большим... |
Долго не мог решиться, как же наводить окончательную
красоту - красить или обтягивать карпетом? Окрашенные таким же методом
подиумы держатся без нарушений покрытия, но ведь в багажнике совсем
другая атмосфера... В итоге остановился на краске, однако прикупил на
всякий случай карпет и клей для него.
Перед финишной
покраской еще раз проверил герметичность ящика водой - ни малейшего
подтекания. Затем внутреннюю поверхность задемпфировал вибропластом, для
лучшего контакта нагрев его феном. После этого наружные поверхности
покрыл антигравием "Body" в два слоя, через
сутки нанес слоя четыре матовой краски с получасовыми перерывами и
оставил сабвуфер сохнуть. Получилось довольно симпатично, ящик черного
цвета визуально стал меньше.
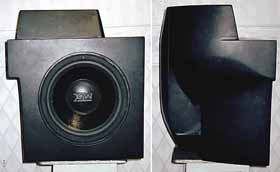
|
Покраска закончена, динамик установлен, а вот провода
пока протянуты "на замазке", без розетки.... Торжественный момент
- изделие готово к прослушиванию. |
Монтаж
Оставались последние штрихи -
установка динамика и разъема. Применить обычные клеммы для провода мне
не удалось, т.к. толщина стенок в нужном месте оказалась слишком велика.
После коротких консультаций применил соединение типа "Canon": вмонтировал розетку в корпус ящика, посадив
ее на герметик. Получилось изящно и очень практично.
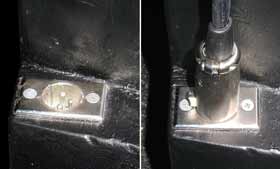
|
Вообще-то это разъем для микрофонов, но его применяют
и для подключения сабов. Герметичной является именно такая пара, с
простой розеткой и фиксатором на вилке, а не
наоборот. |
Для крепления динамика к передней панели использовал
саморезы, предварительно засверлив отверстия двухмиллиметровым сверлом,
иначе фанера могла бы потрескаться. Герметизацию применил проверенную,
при соблюдении технологии гарантирующую отличные результаты - с помощью
силиконового
герметика.
Закрытый ящик проверить легко - негерметичная
конструкция начинает "свистеть" каждой дырочкой при надавливании на
диффузор; недопустимо также, если он достаточно легко утапливается
внутрь. Диффузор должен упруго пружинить и при отпускании руки сразу
возвращаться на место. Иначе все усилия теряют смысл.
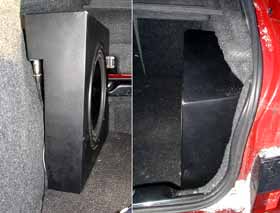
|
Слева вид на сабвуфер изнутри багажника, справа - вид
снаружи. Ящик не занимает много места, компоновка получилась
компактная. Вилка разъема очень удачно спряталась в
уголке... |
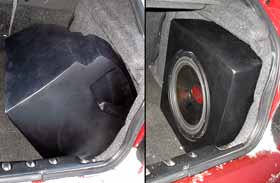
|
На полпути к месту установки, именно так приходится
засовывать ящик в свое гнездо. Справа - окончательная
установка, так и катаюсь... |
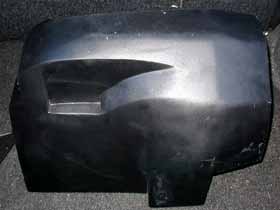
|
Сабвуфер в багажнике "лицом в пол". Да, когда он вынут
из своего места, то выглядит гораздо масштабнее... Краска
успела кое-где повредиться, но белесые пятна спереди - это иней.
Мороз на улице, однако... |
Для окончательной установки сабвуфера в багажник пришлось
подрезать коврики пола и арки колеса. Заодно оклеил вибропластом
металлические поверхности - арку колеса и прилегающие к ней области.
Ящик помещался на своем месте без особых усилий и держался уверенно за
счет собственного веса, поэтому дополнительное крепление делать не стал.
Будет вываливаться - сделаю. Также пока не сделал защитную решетку для
диффузора, какой формы и из чего - не
придумал.
Выводы
Относительно звука. Сначала я
установил и пользовал старый динамик MTX, затем
решил попробовать другой брэнд - Cervin-Vega!, модель HED. И тот, и другой динамики играют в этом ящике
отлично, разумеется, с разными коэффициентами общей добротности системы;
на новой головке слышно и 20 Герц, и турецкий барабан. Впрочем, никаких
более точных измерений я пока не проводил, но в плане звука ящик
оправдал себя на 100%, в этом нет сомнений.
Что касается
технологии, то я бы отметил данное произведение как "нерекомендуемое к
повторению", в первую очередь из-за огромных трудозатрат. Когда я
осознал весь объем работы, было уже поздно - фанера закуплена и часть
уже порезана. К примеру, обработка одного слоя фанеры (примерить,
вырезать снаружи, подогнать, скрепить, <skip>, вырезать внутри,
подогнать, скрепить) занимала в среднем от 45 минут до часа. То есть
фактически одна рабочая неделя (40 часов) ушла на каркасные работы.
Остальное, конечно, несоизмеримо по трудозатратам, но тоже требует
ресурсов. На основную часть работ у меня ушло около трех недель, на
остальное - еще парочка. За такое количество рабочего времени я бы
вылепил парочку стеклопластиковых "стелсов"!
Себестоимость тоже
немаленькая, порядка 80 уе с учетом насадок на дрель, расходников и
фрезы. Эпоксидки ушло практически столько же, сколько и в прошлый раз. Фанерный
ящик получился намного тяжелее своего стеклопластикового
предшественника, правда, никаких претензий ни к прочности, ни к
жесткости конструкции не предъявишь. Другими словами, второй раз я за
такое не возьмусь и другим не советую. Но с другой стороны, если есть
время и желание, то почему бы и нет?
Продолжение следует.
Главная
Назад